How digitalisation helps solve energy and comfort issues – The story of the Blue House
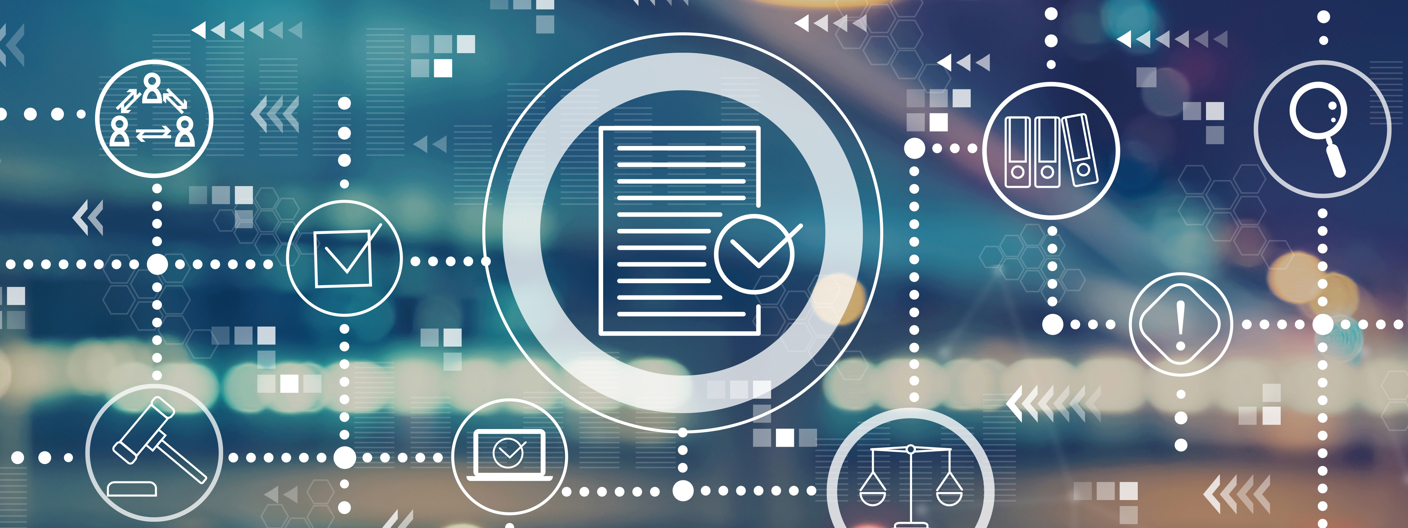
The Blue House project is an example of an ambitiously sustainable, energy-efficient and innovative building. With the motivation to create modern, attractive and flexible office space for the tenants, the building owner worked closely with the HVAC supplier and the design consultant to create such a solution. Thanks to state-of-the-art technology, the project was fine-tuned to meet the property owner's requirements for a good indoor climate, energy efficiency and digitalisation. A team of highly experienced HVAC professionals contributed with their expertise throughout the process, from the initial design phase to operation and optimisation.
We will explore several key aspects of the Blue House project
- The building's journey - from the original design to the final result with applied changes.
- The advantages and challenges of designing a two-pipe change-over system.
- The comparison between calculated energy demand during the design phase and the building's actual energy use, as well as the measured data from the continuous monitoring system.
- The role of digitalisation will be highlighted in the success and also be significant in the survey findings throughout the project.
- The importance of understanding monitoring of a demand-controlled HVAC system, as well as the implication of future legislation for all buildings with such products and systems.
The background of this project – Early supplier involvement in the project
The returning client aimed for a future-proof building with good indoor environmental quality, energy efficiency, sustainable materials and minimal risk of not meeting targets. Suppliers with immense HVAC expertise was therefore involved early in the design phase which was vital to influence the design and delivery of efficient systems which were to incorporate novel and cutting-edge technologies.
The Blue House's building envelope was constructed with insulated, thick concrete walls and reasonably small windows with internal shading to reduce heat loss. Different constructions have U-values, resulting in a total overall U-value of 0.25 W/(m2.K), well below the national building design requirements of 0.6 W/(m2.K). This makes the Blue House twice as good as the national requirements. However, today's national requirements are revised to be below 0.5 W/(m2.K).
The building envelope was a key element for the energy performance thanks to its insulation capabilities, however, a focus on HVAC was the fundamental prerequisite for achieving a low energy consumption.
The original technical solution for this building has changed considerably in the final design
The original plan was to use climate beams for ventilation, cooling and heating (meaning there would be no need for radiators on walls). The suppliers intended to use a chiller and heat pump but switched to an irreversible heat pump for heating and cooling. This meant changing from a four-pipe system to a two-pipe change-over system, which is quite unusual in the Nordic countries. To handle the need for simultaneous heating and cooling, the climate beams in the conference rooms had to be oversized to provide air quality for higher occupancy and to allow for the use of free air cooling - in contrast, the rest of the building would need heating.
Suppliers suggested using demand-based water temperatures to match the components and improve the performance of the reversible heat pump. The air handling unit also had some unique selections, such as an absorption rotor, which reduces the size of the reversible heat pump and further reduces the cost of carbon footprint. Slightly oversized radiators were also needed in some areas that were not ventilated.
All active components have sensors for continuous indoor climate control – occupancy, temperature, air quality with VOC sensors, and relative humidity in some spaces. Ventilation in the building is demand-driven, so the available pressure through the air handling unit is always as low as possible. Heating and cooling are also demand-controlled, meaning that the valve positions in the system are monitored and constantly optimised with water temperature. Communication with the building management system is wireless, with components connected via Ethernet cables and Modbus. All components are connected to a cloud service for monitoring, analysis and troubleshooting.
Revised building regulations meant changes
During the project, stricter building regulations BBR29 were introduced in Sweden, affecting energy performance classification and weighting in factors for purchased energy for the Blue House. Initially, the calculated performance of the building ended up in class B, when the project aimed for 32 kWh/(m2.a). After the building was occupied, the Energy Performance Certificate (EPC) based on calculated data resulted in class C, based on the new stricter regulations in BBR29. Based on last year's measured data, the reassessment showed energy class B at 25 kWh/(m2.a).
Meeting stringent building regulations and achieving a higher energy rating can increase the property value, and the property owner/investor of this building may be eligible for lower mortgage rates, such as the so-called green/sustainable mortgage, leading to more significant investments. With better energy performance, the chances of attracting and retaining tenants prioritising sustainability and low energy use will increase, thus raising rental income. A good EPC rating, reporting energy consumption and offering energy data to tenants also have great value through ESG reporting for larger companies for offices for rent.
Embodied and operational carbon for the Blue House
The property owner´s vision was to create a sustainable building with minimised embodied carbon (from the construction of a property and building systems, including the HVAC installations) and operational carbon (the building's energy use). By removing radiators from the system, 5,000 kilograms of carbon dioxide equivalent emissions were saved, and switching to a two-pipe changeover meant a further reduction of 800 kilograms of CO2 emissions. All in all it results in approximately three kilograms per square meter of reduced embodied CO2 for the building.
To achieve this zero-emission building, in line with the vision for Europe and the new EPBD, more realistic and accurate input data for calculations from the project's beginning were essential and significantly influenced the margins for error. Stricter energy performance requirements can lead to suppliers and energy assessors needing to improve the accuracy of all building components and calculations. That is especially important when building systems and specific components are highly complex, so closer collaboration between everyone involved in the project was one of the key elements.
Optimising functionalities for higher energy savings and better comfort
The building owner wanted the best possible indoor environmental quality. The results from the monitoring show that the temperature is within limits for more than 95% of the time, and this goes for all rooms in the building. The VOC level, or the air quality, are fair or better for more than 97% of the time in the building: This meets the demands regarding indoor environmental quality.
Great effort has been put into creating a comfortable indoor environment in terms of thermal, visual, sound quality, and comfort. The building owner prioritised great tenant workspace satisfaction, and the building is partly rented as flexible office space, maximising occupancy.
From analogue to digital – solving issues efficiently saves time and money
The EPBD recasts demands for building owners to monitor their buildings, analyse them, and provide performance data for everyone. Using digital tools offers significant advantages. It allows access to all data from building systems (DCV systems, air handling units, monitoring functionalities and more). It can provide a complete overview of the building, including data points from room level to temperature delivered from the chiller and air handling units. All done remotely to save time and money.
Historically, consultants spent a lot of time adjusting building systems and many issues were too complex to notice until someone complained. Digitalisation is now an essential and effective tool that helps to save resources and deliver faster results, this by identifying problems remotely and again, save time and money. It also benefits tenants by not disturbing them at their workplace.
Fine-tuning is a way to use digital tools efficiently and to spend less time on manual inspections as locating/accessing the correct components can be done quickly. In the future, when utilising DCV systems with multiple components, service engineers must be granted good access to adjust/replace to ensure that the building works as intended during its entire operational lifetime.
Fine-tuning, along with experience and knowledge, is essential
Digital systems and wireless capabilities can help with immediate adjustments needed for system remote alternation, stabilisation and optimisation of building systems. The combination of tracking, knowledge and experience with digital tools in the service organisation will be key in the future.
Using digital tools with historical log analysis can help with analysing parameters and functions of building systems to achieve optimal operation. This can lead to energy savings over the system's lifetime and prolong the lifetime of all building components.
Summary
Meeting the 2050 targets to reduce Europe's buildings to zero-emission buildings will require early engagement from everyone - clients, designers and suppliers. Partnering early is vital as suppliers could provide consultants with outstanding data and information about functions. Creating sound systems is essential and digitalisation is key during the design and operational phases.
The HVAC experts must be able to use advanced tools to select the right systems for the right projects. Buildings must be demand-controlled from the room components to the building system. To find solutions that perform as intended, more effort must be put into energy usage and efficiency of buildings and systems. All building components must be energy-efficient, interactive, and data-driven to deliver saving potential. Remote access can help identify problems and react quickly. Visualisation of indoor climate and energy performance needs to be more precise than we generally do today.
Reference
This text is based on the Swegon Air Academy webinar: 'The Blue House with green ambitions - The importance of monitoring advanced HVAC systems to optimise energy efficiency and indoor climate' with Ulf Hörman as Business Development Director at Swegon, Eric Johnson as Technical Design Engineer at erelko AB, Anders Hultman as Project Systems Engineer at Swegon, Robin Svensson as Service Engineer at Swegon and Åsa Norén-Lundh as Indoor Environmental Competence Manager acting as the moderator from the Swegon Air Academy.